Construction company executives have a lot to worry about. We find that CEOs leave a few key risks unchecked.
1. Being Unprepared for a Crisis
A crisis is any unpredictable event that threatens to harm an organization, its stakeholders, or the general public.
What's the risk? The credibility and reputation of an organization is heavily influenced by how the company responds during a crisis. Failing to have an effective communication plan in place could be detrimental to your company's image in the community and create confusion amongst employees.
What can you do? Make sure to have a crisis plan in place which does the following:
- Defines and assigns the crisis team.
- Outlines roles and responsibilities of the crisis team.
- Details steps to take in the event of a crisis.
- Indicates who to contact, resources that are available, and procedures to follow.
- Provides a platform for training, testing, and improvement.
How to implement a crisis communication plan.
2. Increasing Competition
Oftentimes, the company that comes in with the lowest bid is going to win the job.
What's the risk? Forgoing safety to decrease expenses is a tempting thought. And though that might work in the short term, in the long term it will inevitably lead to a costly accident.
Falls are the top cause of construction fatalities and account for a third of on-the-job deaths.1 When a worker falls at a job site, it can cost on average over $100,000 per claim just in work comp costs alone.2 When hefty fines like this hit your business, it's impossible to keep bids low when paying for such catastrophic claims.
What can you do? Having the ability to bid competitively all boils down to having the right safety program in place. Educate workers on fall safety and ensure you have the proper equipment in place. Investing in fall safety equipment could be the difference between scoring your next client or being left in the dust.
ORANGEPAPER: Contractor Management Services - how your safety success drives business
3. Labor Shortages
Skilled labor is becoming increasingly more difficult to find.
What's the risk? During the recession, a lot of the construction workforce was forced to exit the industry to find other jobs. Between April 2006 and January 2011, nearly 40% of construction jobs were eliminated - that's nearly 2.3 million jobs. Many of those workers never returned to the workforce - even as the economy improved.3
What can you do? Developing a job training program for not only new, but current workers can bridge the gap between willingness to learn and having skilled labor. This will allow you to get new employees up to speed while also making sure your existing labor remains sharp.
4. Cyber Attacks
Cyber attacks are a new reality and even the most established companies have proven to be unprepared.
What's the risk? Given the increasing popularity of Building Information Modeling, Integrated Project Delivery, and file sharing, contractors are more vulnerable than ever before. While all of these innovations are certainly moving the industry forward, they are leaving you exposed.
Hackers can access designs, security systems and features, financial information, project-specific information, and your employees' personal information (think social security numbers).
What can you do? The biggest risk for a cyber-attack is your employees. Develop a Written Information Security Program (WISP) which outlines security measures and also discusses the security measures employees should take, best practices, and complies with regulatory requirements.
It is also smart to prepare an Incident Response Plan that is the blueprint for what to do in the event of an attack. This will limit your exposure and expenses that result from an attack.
Cyber insurance is also available to protect you when preventative measures come up short.
5. Business Interruption
What's the risk? The construction industry has the highest fatality rate of any industry in the United States.4 This leaves little room for acting risky while on the job site, especially when the costs following an accident rack up quickly.
Unsafe acts lead to equipment repairs, costly claims, and employees out on leave. In addition to the human costs following an accident, your business also takes a hit. It is estimated that for every $1 of direct costs, there is $3 of indirect costs which include:
- Time lost from work
- Loss of efficiency
- Damage to tools, equipment, and other property
- Loss of or slowed of production
- Failure to meet project deadlines
- Training costs/replacing workers
- Medical expenses
- Wages
- Worker's comp premiums
- Legal issues
What can you do? Safety needs to be at the root of your company's culture. Employees need to be properly trained, have a clear understanding of safety objectives, and be held accountable for all actions.
Train all employees on the importance of safety and the part they play as individuals - setting a risk ownership mindset. Workers who understand the "big-picture" part of safety are more likely to follow your company's objectives.
Find out how one company instilled a "safety accountability"
mindset into their culture: hni.com/stories/poblocki
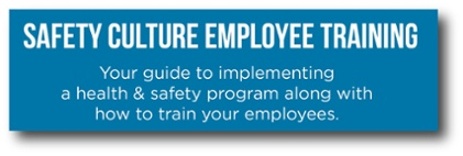